While software-based advisory procedures and cybernetic self corrective processes have advanced the mould-material-machine paradigm for plastic injection moulding, some constraints still remain in the trajectory towards further improvements and cost savings. Read on to know more.
IM process development has seen steady progress towards optimizing the mould-material-machine paradigm. Software-led advisory process developments, such as Moldex, Pro-E mould, and mould flow simulation have helped eliminate defects and predict cycle time accurately even before the mould is manufactured. While these have been very useful and are now among the mainstream applications of the technology in injection moulding, only a few players have progressed to optimization of DOE-based software. Software such as Sigmasoft, Nautilus make it simpler to narrow down the process window, enables a good understanding of constraints and solutions available, and encourages a one-time set-up study to save time for any future process corrections. Yet a step further are the cybernetic self-corrective process algorithms which build negative feedback loops to ensure that the process is always close to the ideal. Energy efficient moulding and sustainable moulding are the baseline goals of the technical managers in the industry.
Given these new methods at hand, what are currently the key constraints of the IM process development? What are the unique ways that we can deploy technological advances to save business costs? We attempt to provide a provoking dialogue through this article to answer these two questions.
While working with EIPL, I have had the unique opportunity to explore the process and product design, and pursue research and optimization. The article is a conceptual outlook on what we see as promising branches for further research, factors that would further build bridges to unexplored fields.
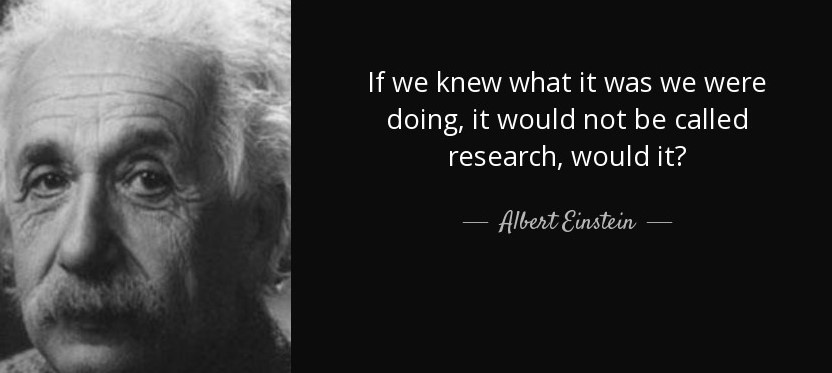
A. NON-STANDARD PROCESS CONTROL/ CALIBRATION- REDUNDANT NEED FOR PROCESS REVALIDATION
There is a great deal of investment made by the customer on process revalidation i.e. to revalidate the process at the converter site to check the results at the mould maker’s site. From an idealistic standpoint, this is a physics problem. Yet it is wishful to attempt to calculate the process settings without physically loading the mould on a different machine. One of the multiple reasons we cannot do so is the unmapped effect of machine parameters and variables on the output of the machine. This is a very interesting area, although a non-transparent and under-researched one. We have used tools and software to predict the filling time and viscosity of the plastic. Although we can model and predict the achieved viscosity in the barrel, we are yet to arrive at definitive answers to mathematically model and predict the different barrel types, screw types, back pressures, and RPM, along with barrel temperatures to predict the viscosity achieved by the material ahead of the screw.
If we were able to do so for a barrel, we could request the IMM OEMs to share the 3D models for the barrel and make a mathematical calculation to predict the process parameters – the process window – for a machine that is completely new vis-a-vis one on which the process has been previously proven, established, or developed. For example, the high-end IMM machine which has excellent feedback circuits and process control, the sophistication of gathering and representing process data on the IMM interface, and the ability to control process points among many methods of IM process control, is desirable for every moulding shop. However, it is not so easy to transfer a mould from a high-tech IMM to one with lower capabilities as the capabilities of the IMM mask and compensate for issues with the mould, cooling circuit design, or other lacunas in the mould, process, or even the material. Thus, transparency and data availability for IMM variables and overall parameters, including the mechanisms of the machine, is key and not just the information provided on the HMI. The IMM remains specialized equipment, similar to the backend of software with little information available to the end user for modification. IMM manufacturers do realize it to be a key to a higher market share and have been the torch bearers of the technological shifts. We, at EIPL have a two-pronged approach toward research in this area- 1. Data analysis and establishing data mining mechanisms, data-generating platforms, and thus the subject matter pruned algorithms to make the best process estimate without making the mould, 2. FEA-based predictive models
B. RESEARCH ON THE RELATIONSHIP BETWEEN MOULD COOLING CIRCUIT DESIGN AND ACTUAL PLASTIC PROPERTIES.
Mould cooling channel design and cooling efficacy are among the most well-researched fields in the industry. With path-breaking advancements such as conformal cooling and simulation-assisted design, the customer is able to pay for and get the optimal cooling channel design that greatly affects the mould temperature and overall CT. As we are painfully made aware that viscosity in the mould is a function of mould temperature, injection speed, starting viscosity in the barrel, and plastic temperature. Also, plastic product properties are a function of plastic shrinkage, viscosity, rate of cooling, and hinge design. The number of dependent and independent variables involved makes it complicated to research the area of cooling optimization. The difficulty to amplify the input/output of controlled and uncontrolled variables makes cooling channel optimization an unenvious research topic to pursue. The resolution of any of these constraints will for sure bring a coveted technological advantage to the mould maker. There have been several attempts to use data analytics and mathematical modelling-assisted decision-making to determine the thicknesses of steel parts. Yet, we are not close to making the technology mainstream enough to be used by every tool maker. The industry is yet to perfect the trade-off between efficiency and overdesign that leads to aesthetic issues.
Such type of design education and the establishment of affordable and effective methodologies will plateau in the coming decade. EIPL has certain data-oriented projects that aim at helping the effort. That brings us to the third key area of design education that is quite prominently established and encouraged, even awarded as a proper area of doctoral research. And yet, it is in a very nascent stage in the injection mould part design industry- design education optimization for CT.
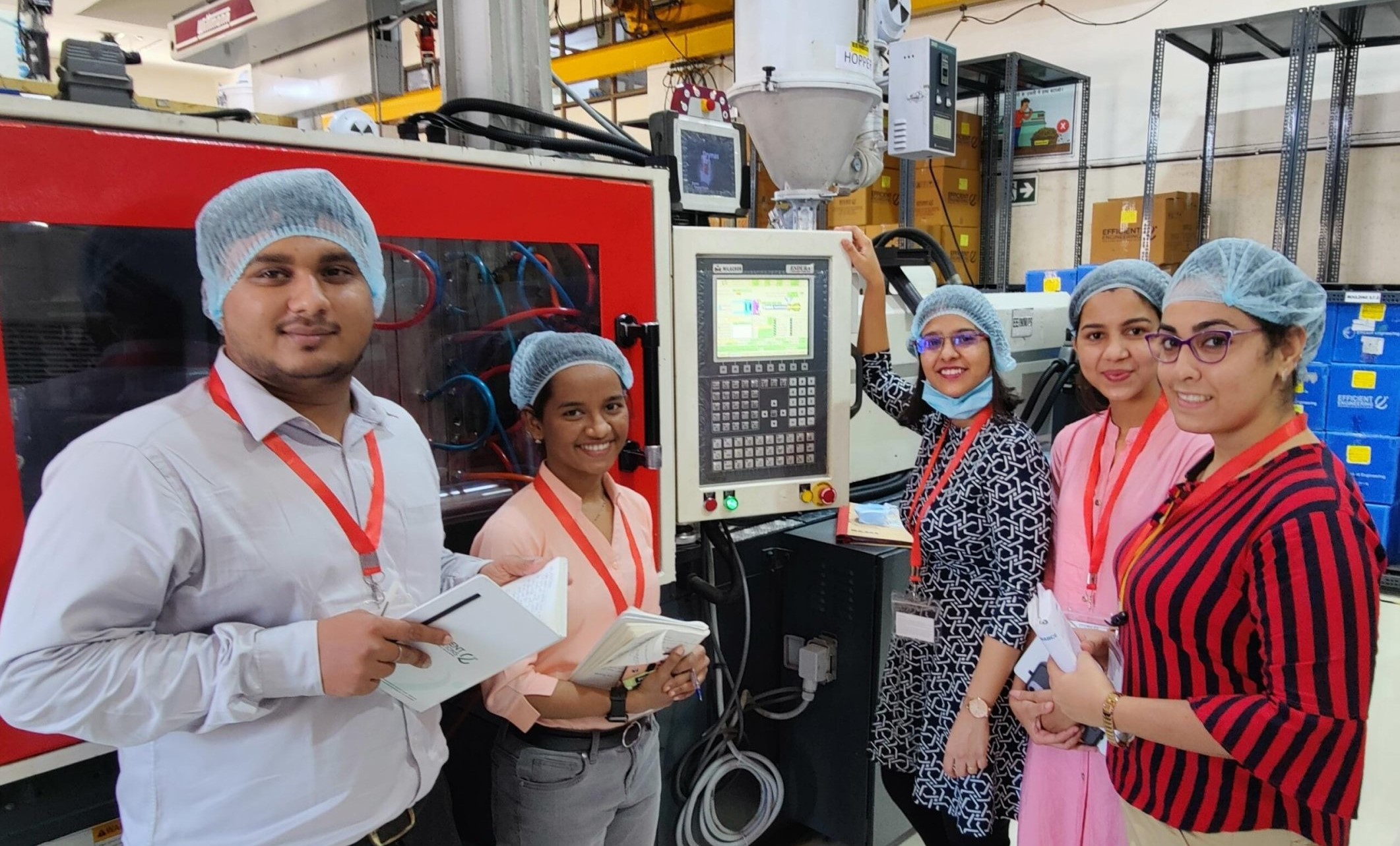
C. PART DESIGN OPTIMIZATION FOR CYCLE TIME
Multiple organizations specialize in part design optimization for the medical and FMCG industries. Though optimizing part design for CT (cycle time) remains a rather experience-based field. There is little empirical evidence suggesting methods to follow in order to achieve optimal results targeted for product designers. The brand and NPD industry would particularly benefit from the research that mould makers or clients conduct for mould design optimization if an integrated systems approach is leveraged across fields. The research available on the topic is case-based and not translated to design guidelines or readily usable engineering rules that designers can use as a parameter when starting a design process.
There are design data books available for mould-ability and aesthetics. We have advanced now to software that can help designers simulate any design defects. What we do not have yet is a design data book for a part design that provides design decision guidelines for a part that reaches a targeted CT. From a business point of view, this would be a very profitable venture, to integrate and make sense of the existing research in the light of part design considerations. If we were to ask the mould makers, they would make many suggestions on the thickness of the part and CT. For example, CT from simulation or a particular part surface finish would help make the same part with lesser hold time, effectively reducing CT. The brand is often married to the product design, missing out on a huge opportunity to save CT and incidentally a huge business cost. The FMCG industry’s time to market is almost always the focus. Therefore, design education is on the back burner. If the knowledge was to be converted to design data books for mould-ability, it would help designers optimize CT that impacts not only the design but also the business.
Efficient Innovations Pvt. Ltd. (EIPL) has been in the business of plastic injection moulding and the improving injection mould process for over decades now. We have also invested in material and processing research. Get in touch with us at www.efficientinnovations.in OR Write to us at radhika@efficientengg.com to know more about how we can help you use our literature study and some of our own research to deliver top-class moulding solutions. .
Watch this space for the Hype cycle for innovations in IM.
By Radhika Sawkar