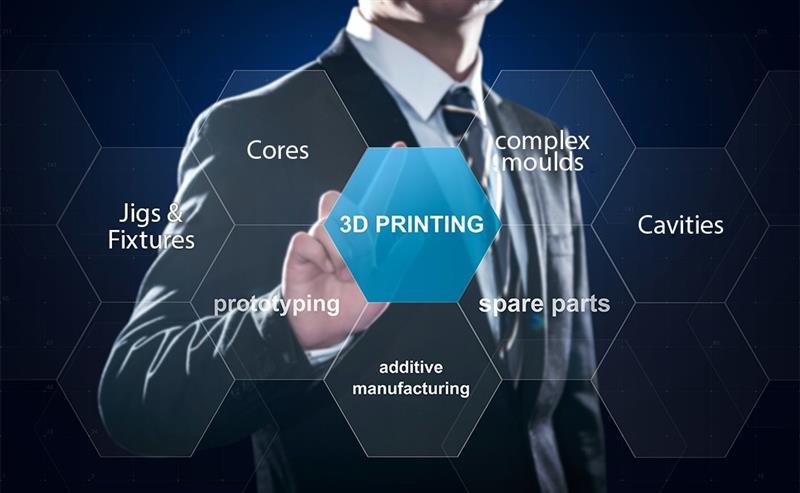
Technology is releasing the creative energies of the engineering designer. This has led to parts acquiring unprecedented complexity. 3D Printing and Generative Design are enabling designers to do more than just deal with these elevated intricacies. What is more, they lend the green, eco-friendly edge to the manufacturing process.
Shifting Sands of Injection Moulding
Economical, scalable, and fast when mass producing parts, even those with complex designs. Reasons enough to account for the popularity of Injection Moulding? There is the other side though. Mould building is, at present, a very lengthy process and depends heavily on the part design. Injection moulding dates back to the 1870s, when the machine and moulds were relatively simple.
Things are vastly different now. Part designs are getting complicated by the day. Mere machining is not enough, precision machining is the order of the day. And everyone wants to reduce the time for part production. As a result, injection moulds are more intricate than ever before.
Consider this:
Manufacturing of core stack has a major impact on the entire tool build network. Courtesy of the lengthy building process. The core stack is the most important part of the mould as it imparts the required shape to the part. Another challenge is to cut the cooling time which hugely influences the cycle time and return on investment (ROI). Traditional machining techniques have their own limitations. These prevent the best possible cooling in close proximity of parts during moulding.
Due to the high demand for plastic parts and high costs of injection moulds, manufacturers are on an unrelenting quest to optimize the cycle time for maximum output and least cavitation.
Designer’s Choice: 3D Printing & Generative Design
3D printing has made it much easier to manufacture mould inserts with complex designs and shapes. The technology also enables better cooling compared to traditional machining processes.
Not long ago, 3D printing was popularly employed to make toys, small plastic parts, and prototypes. Advancements in material technology have allowed 3D printing of metals for industrial applications. Due to high precision, we can achieve well defined tolerances required for FMCG and automotive applications.
The method has proven particularly useful in making parts with variable thicknesses. Designing such moulds is equally complex and that is where generative design comes in. Generative design used together with 3D printing facilitates production of complex moulds with intricate cooling channels.
Generative design utilizes Artificial Intelligence (AI) and the designer-prescribed constraints to generate various design options for intricate parts. With the multiple available alternatives, the designer can choose the design which delivers on the most important criteria. This is relevant where the design digresses from the one originally imagined. Most of the popular Industrial CAD organizations have already incorporated generative design into their software. And, the concept is now leading a design revolution.
Design Parameters & the Green Edge
Engineers normally furnish these design constraints:
- Physical Constraints: Are the basic information fed to the CAD software for design creation. It includes the weight and the size of the parts, plus information regarding areas that the part should not occupy.
- Forces, Pressures, and Loads: This helps the algorithm decide where the part needs reinforcement based on the stress affected areas. Based on the load and induced stress, the software will add more material in high-stress areas and vice versa.
- Material of Construction: Assists the program understand the design freedom available for the creation of the file. Most importantly, we need to keep in mind the material grades available for the 3D printing process and the properties of the plastic material of construction.
- Manufacturing Process: Additive manufacturing or CNC machining? Taking this call is essential, as it must be a manufacture-able design. Efficient Innovations has supported clients with moulds that involve 3D Printing as well as CNC Machining.
That apart, manufacturing with 3D Printing and Generative Design slashes material consumption making. This makes the production process sustainable, and economical while delivering low-weight parts.
Summing Up
In addition to upgrading the mould design, such a manufacturing process can churn our complex part designs. Its environmental impact will be minimal due to lesser waste generation. As the process develops further and takes centre stage, we will witness its expanded adoption by major players in the injection moulding industry.
Efficient Innovations believes in staying ahead of the times. To know more on how we harness the incredible prowess of 3D Printing for state of the art plastic moulding, contact us at www.efficientinnovations.in
We are waiting to hear from you!